Injection molding stands as one of manufacturing’s most versatile processes, yet it presents unique challenges that separate industry leaders from the rest. This precision-driven technique, while delivering exceptional results, requires expertise to overcome its inherent difficulties.
Material selection represents the first major hurdle. Engineers must balance mechanical properties, flow characteristics, shrinkage rates, and cost-effectiveness. A polymer perfectly suited for one application may prove disastrous for another, requiring deep material science knowledge to make optimal selections.
The mold design phase introduces another layer of complexity. Creating tooling that accommodates proper gate placement, runner systems, cooling channels, and ejection mechanisms demands experience and foresight. Even minor flaws in mold design can cascade into production nightmares—from incomplete fills to excessive flash or warping.
Process parameter optimization remains perhaps the most challenging aspect. Balancing injection speed, pressure, temperature, cooling time, and cycle duration requires precision that comes only through experience. The interdependent nature of these variables means adjusting one parameter inevitably affects others, creating a complex balancing act.
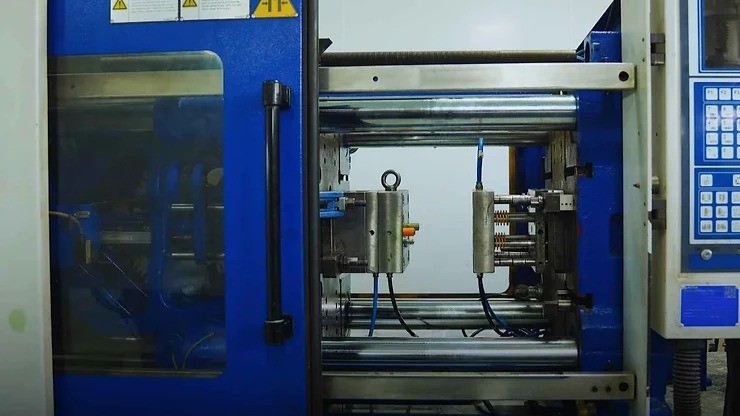
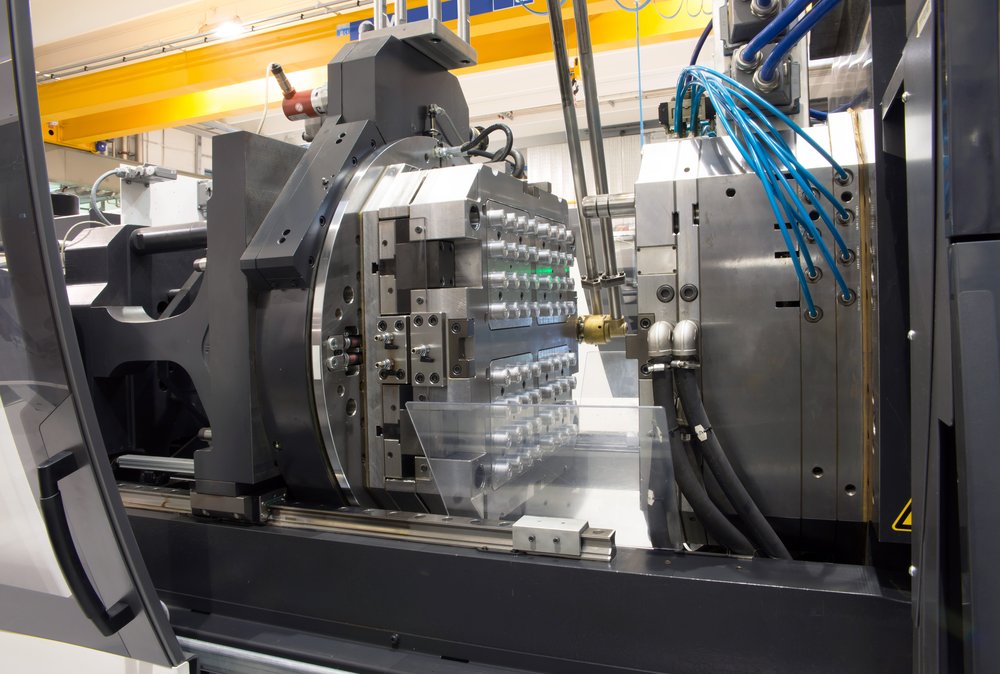
Quality control presents ongoing challenges. Parts must maintain dimensional stability, appearance standards, and mechanical integrity. Identifying and resolving defects—whether sink marks, flow lines, or internal stresses—requires both technical expertise and systematic troubleshooting methodologies.
Scale-up difficulties emerge when transitioning from prototyping to mass production. What works perfectly in small batches may encounter unforeseen issues at production volumes, necessitating careful planning and validation procedures.
Raamps Group has systematically overcome these challenges through investment in advanced simulation software, precision tooling capabilities, and rigorous process validation protocols. By embracing these difficulties as opportunities for innovation, they’ve established Clixroute as a problem solver in the injection molding space.
For manufacturers seeking reliable injection-molded components, understanding these challenges highlights the value of partnering with experienced providers like Clixroute who have mastered the delicate balance of material, design, and process optimization that defines injection molding excellence.